Research Tasks
The POLKA project is divided into 15 research tasks. Each task is a 36-month PhD project for an ESR (Early Stage Researcher).
Click on the research topics below to find out more.
Each task is part of a work package; there are 5 work packages in all.
Work package 1: Passive instability control
A thermoacoustic instability can be suppressed for a range of operating conditions by a carefully positioned perforated plate in the combustion chamber. This is because a perforated plate not only absorbs but also re-distributes the acoustic energy, and as a consequence it can disrupt the thermoacoustic coupling that excites the instability. This WP will conduct a systematic study of perforated plates and their effectiveness for instability control. Micro-perforated plates (MPPs) offer a particularly good prospect because of their superior sound absorption ability, which is due to their large number of sharp-edged holes. The exact sound absorption mechanisms are still not clear, especially in the extreme situations found in a combustion system: hot conditions and grazing flow will be examined in task 1.1, while high pressure amplitudes and out-of-plane plate vibrations will be examined in task 1.2. Task 1.3 will focus on the question how best to install perforated plates in a combustion chamber so as to maximise their effectiveness.
Work package 2: High-resolution/reduced-order simulations for hydrogen combustion dynamics
This WP will produce fast and accurate numerical codes to simulate hydrogen flames in various combustion systems. Combustion CFD is challenging because combustion is a multi-scale problem with length scales ranging from less than 1mm (flame front thickness) to more than 1m (acoustic wavelength). Several methodologies with varying degrees of resolution and corresponding numerical effort are available, but with standard commercial combustion CFD packages, there is always a trade-off between accuracy and cost. We side-step this problem by a hybrid approach: High-fidelity simulations will be performed for the complex components of the combustion system (e.g. for a turbulent flame), and from the results a simplified description of the component will be extracted in terms of an input-output element. A low-order model will then be developed to simulate the whole combustion system. Recent work at TUM has demonstrated this hybrid approach for nonlinear thermoacoustic oscillations in a laboratory test rig with a laminar slit flame. Using this hybrid approach, task 2.1 will develop scaling laws for various physical processes affected by hydrogen content in the fuel. Task 2.2 will develop fast CFD simulations for a laboratory-scale combustion test rig, and task 2.3 will do the same for an industrial-scale combustion test rig.
Work package 3: Analytical simulations of nonlinear interactions
Analytical simulations involve idealising a physical system and developing an abstract model that describes the salient features of the system. Applied to a combustion system, such models give insight into the web of physical processes and interactions. Also, they give rough-and-ready predictions for parameter studies. An interaction of particular interest is that between flashback and thermoacoustic instabilities. This is a complex nonlinear problem, which will be studied in task 3.1. Another interaction of interest is the nonlinear interaction between different thermoacoustic modes, which is responsible for the phenomenon of mode-switching: an originally unstable mode becomes stable, while another mode with a different frequency becomes unstable. This can potentially be exploited to suppress dangerous modes (i.e. modes whose frequency is close to the resonance frequency of one of the combustor components). Task 3.2 will explore this approach. Task 3.3 will optimise the mode-switching strategy.
Work package 4: Early detection of instabilities and flashback
Thermoacoustic instabilities and flashback can occur "out of the blue" and cause expensive damage to a combustion system. This is particularly true for hydrogen combustion. It is therefore important to develop fast diagnostic techniques that can be used to monitor a combustion system and assess its proximity to instability and/or flashback in real time. Task 4.1 will develop an early-warning system that operates in the linear regime, by using an effective damping coefficient as diagnostic signal. Task 4.2 will exploit multi-dimensional data sets to construct a mode-based precursor in the nonlinear regime. The approach in task 4.3 will be based on temperature monitoring in combustor components threatened by flashback.
Work package 5: Boiler design
The injection of hydrogen into the gas network is a novel decarbonisation approach, which is currently being trialled by a number of sites in Europe, e.g. at Keele University, where the aim is to inject up to 20% of hydrogen into the gas network. A rather more ambitious target is to convert the gas grid to 100% hydrogen, as is being planned, for example, by the UK city of Leeds. With this prospect on the horizon, major technological innovations are required: new types of boilers need to be developed that can be operated on a wide range of hydrogen concentrations (ideally 0 – 100%) in the fuel. This work package has been designed to underpin such innovations. The first two tasks have a high technology readiness level: task 5.1 focuses on industrial boilers, and task 5.2 on domestic boilers. Task 5.3 is more fundamental and will investigate the potential of finned tubes (a common design element in boilers) to suppress thermoacoustic instabilities.
The 15 research tasks and 5 work packages are interlinked as shown in the image below.
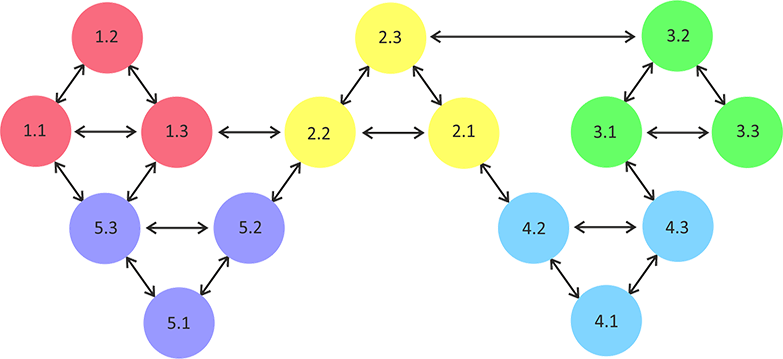